Experiencing a pneumatic cylinder air leak can be a daunting issue for anyone relying on these components for their industrial or mechanical systems. Air leaks in pneumatic cylinders not only reduce their efficiency but can also lead to greater operational costs and potential system failures if not addressed properly.
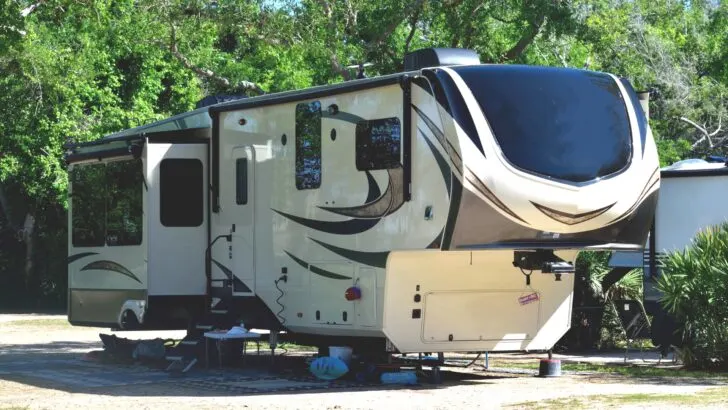
Pneumatic cylinders, fundamental to numerous industries, utilize compressed air to produce a force in a reciprocating linear motion. They are pivotal in mechanized manufacturing processes, robotics, and automated systems across the globe. As these cylinders operate using air pressure, even the smallest leak can cause a significant drop in performance, leading to decreased productivity and increased energy consumption.
Drawing from my years of expertise in pneumatic system maintenance, one of the most telling signs of a cylinder air leak is a noticeable drop in system pressure without any increase in system demand. You might also hear hissing sounds coming from the cylinder itself. Regular maintenance checks are crucial in detecting leaks early.
Conducting a 'soap bubble test' on your pneumatic connections can help identify leaks. By applying a soapy water solution to suspicious areas, leaks can be identified by the formation of bubbles, a clear indication of escaping air.
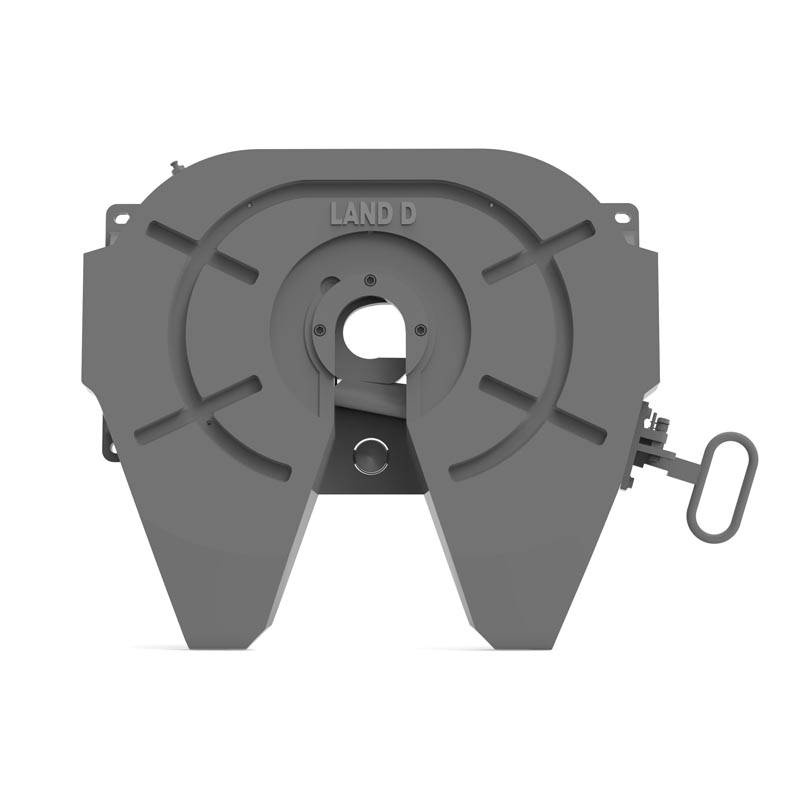
Why is it vital to address an air leak immediately? Firstly, leaking air from pneumatic cylinders results in a decrease in system efficiency. When air escapes, the system needs to work harder to maintain required pressure levels, leading to higher energy consumption. This inefficiency not only drives up operational costs but also accelerates wear and tear on system components. Furthermore, continuous leakage can lead to pressure drops severe enough to cause a system shutdown, leading to costly downtime.
From the perspective of expertise, it is imperative to understand what typically causes these leaks. The main culprits tend to be worn-out seals and fittings. Over time, seals can degrade due to the repetitive motion and pressure fluctuations inherent in cylinder operation. Complex factors such as suboptimal installation, damaging environmental conditions, and lack of routine maintenance can expedite this degradation. Thus, implementing regular check-ups and seal replacements can enhance the longevity and reliability of your pneumatic systems.
pneumatic cylinder air leak
When discussing solutions, ensuring the use of high-quality components cannot be overstated. Investing in seals and fittings from reputable manufacturers guarantees better performance and durability. I recommend keeping a detailed maintenance log for your pneumatic system. Documenting maintenance and any repairs or replacements can provide insights into patterns of wear and predict future needs before a critical failure arises.
Furthermore, integrating condition monitoring technology can bolster trustworthiness in pneumatic systems management. Advanced pressure sensors and monitoring devices can offer real-time data on system performance, catching leaks that might not be immediately evident through traditional auditory or visual inspections. Automated systems can be programmed to alert operators of pressure irregularities, allowing for rapid response and minimizing downtime.
On authority, collaborating with certified pneumatic system professionals for routine inspections and updates can greatly benefit any operation reliant on these components. Experienced technicians can offer tailored solutions specific to your operational needs, identifying potential issues before they escalate. A partnership with experts ensures your systems remain in optimal condition, reducing the risk of air leaks and improving overall productivity.
Ultimately, maintaining pneumatic cylinders, particularly regarding air leaks, requires a comprehensive approach focusing on prevention, quality components, and expert involvement. The potential operational efficiencies gained by minimizing air leaks can significantly impact economic performance, making the investment in quality maintenance and components a wise decision.
This article serves as a guide for industry professionals seeking to comprehend and combat pneumatic cylinder air leaks, ensuring efficiency, safety, and cost-effectiveness in their operations. As these components are integral to numerous operations, addressing air leaks with expertise and practical solutions leads to improved reliability and productivity in any setting reliant on pneumatic technology.